Lithium demand for electric vehicle batteries and energy storage is not only on the rise but also expected to grow by three times from 2024 to 2030, which means an increased lithium supply is needed. Current production methods, however—methods such as hard rock mining and conventional brine mining—are often inefficient, expensive, time-consuming, and majorly impactful on the environment.
The answer is yes, but we need to minimize land, water, energy, and chemicals usage to produce the most sustainable battery-grade lithium. In other words, we need a holistic lithium production process that can optimize all the systems and technologies involved.
Understanding conventional lithium production
Today’s most popular method of lithium production is the extraction of lithium from brine. Although most aquifers contain lithium, only a few have concentrations that are economical using traditional methods. These brines are typically found in arid or desert environments with high levels of water stress. The process includes pumping the brine from subsurface aquifers into massive ponds and letting the water naturally evaporate, a process that takes an average of 18 months. Chemical reagents are then used to extract the lithium from the remaining minerals.
As the water evaporates, the lithium is concentrated and extracted, but only about 30% to 50% of the brine’s original lithium content is ultimately produced. Salt and other minerals precipitated from the brine sit in mounds alongside the evaporation ponds as waste (called tailings), while used chemicals are left at the surface. This creates significant environmental degradation that impacts both native biodiversity and indigenous communities.
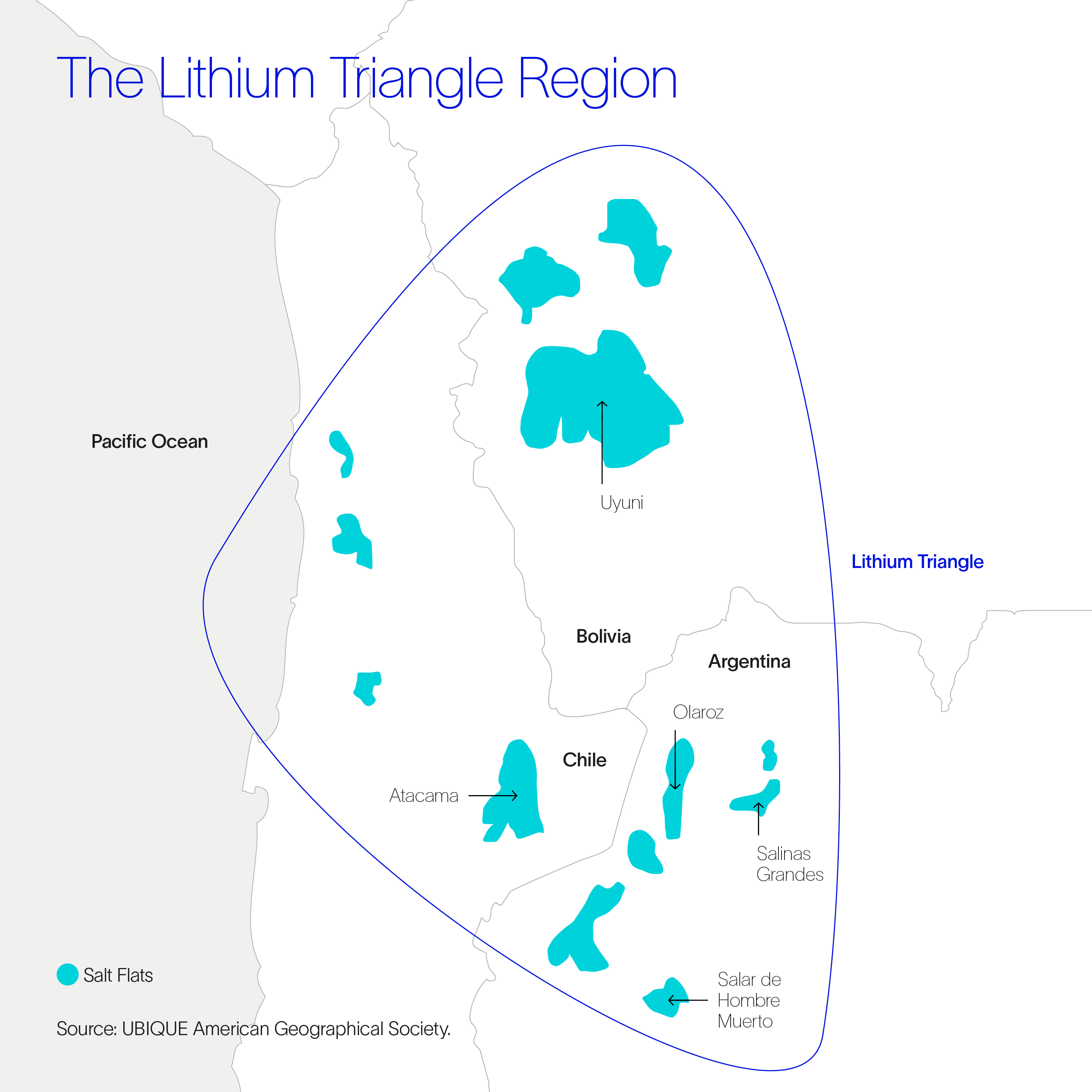
The Lithium Triangle shown above—comprising salt flats or salars in Argentina, Bolivia, and Chile—is the world’s largest lithium reserve. (Imagine the land footprint and chemical reagents required, total water evaporation, and total time spent.) Chile’s Salar de Atacama, for example, boasts one of the highest-grade lithium deposits and oldest significant lithium mining operations in the world. Its lithium-rich brine consists of 37% salt and 63% water.
As mentioned, lithium enrichment into a commercial salt product is achieved by pumping brine from underground reservoirs and processing it in a series of open-air evaporative ponds to precipitate unwanted impurity salts. But given that 90% of the brine water is lost during this evaporation, it takes about 100 cubic meters of water lost to produce one metric ton of lithium carbonate. In 2023, for instance, the Atacama produced more than 200,000 metric tons of lithium carbonate equivalent (LCE), meaning that more than 20 million cubic meters of water was ultimately lost.
Emerging, sustainable lithium production
Sustainable lithium production involves identifying and modeling both lithium reserves and aquifer behavior, and it’s important for several reasons. Innovative lithium extraction and water management tech can accelerate lithium production, recover more lithium from the brine, use less water, and return most of the spent brine to the aquifers to minimize environmental impacts.
Accelerating and maximizing lithium recovery
In recent years, several direct lithium extraction (DLE) technologies have emerged. According to one of Goldman Sachs’ Global Metals & Mining reports, DLE is “a potential game changing technology” for lithium supply given its ability to double lithium production, use less water, and reduce land utilization to less than 10% compared with conventional evaporation ponds. Not to mention this technology enables access to lithium in areas where evaporation ponds are not feasible.
The central idea behind DLE technologies is the direct and continuous extraction of lithium from pretreated brine through a thermal or chemical process. Not only does this shorten processing times and improve recovery rates, but it also yields both lithium and spent brine. After the extraction process, up to 90% of that brine—with identical chemical characteristics minus the lithium—can be reinjected into the aquifer, thereby minimizing the impact on local water tables and ecosystems.
Benefitting from these technologies requires a comprehensive approach to sustainable lithium production that includes subsurface studies. These help us understand the lithium that’s in place, sweet spots for production, and reinjection pattern options. Once production and reinjection start, it’s important to monitor well and overall field performance, while continuously updating the models to both improve lithium production and minimize the impact of dilutions.
This is where fit-for-purpose tech and historical information from oil and gas fields (where available) come into play. They can provide information on
- behavior of the subsurface aquifer
- brine composition
- lithium concentration
- potential mixing of fluids at the freshwater-brine interface
- impact on the water table.
Leveraging desalination for freshwater production
Given that DLE only extracts lithium, the result needs to be concentrated further to ship lithium chloride, or it must go through a crystallization process to produce battery-grade lithium carbonate or hydroxide. Sustainable approaches to lithium extraction typically include a step where novel versions of these concentration technologies are used to improve water recovery and reduce energy usage.
One of these approaches leverages desalination tech to both concentrate the lithium chloride and produce freshwater from the pumped brine. The freshwater can then be used in any pre- or post-treatment of the brine, thereby eliminating the need to tap additional freshwater aquifers for processing.
In addition, by recycling the freshwater in a closed loop system, the lithium production process can be self-sustaining. Up to 90% of water in the form of spent brine can be returned to the aquifer, thus reducing the environmental impact on nature and communities.
Reducing land usage and environmental impact
Another concern associated with the evaporation method is the significant amount of land it requires. In the Atacama, for example, it takes between one-tenth and two-fifths of an acre of land to produce one metric ton of lithium. At production rates of 121,000 metric tons of LCE per year, more than 17,000 acres of Atacama desert land are required (a figure that only considers the size of the evaporation ponds).
With DLE technology, there’s no longer a need for evaporation ponds. The physical footprint of the extraction facility is estimated at less than 10% of the evaporation ponds, and—considering that recovery yields double—the equivalent land usage is less than 5%. This would be equivalent to producing the same amount of LCE in the Atacama but with a footprint of less than 1,000 acres. A smaller footprint from these novel lithium extraction processes ensures minimal impacts on the surface, leaving more of the natural environment for local flora, fauna, and people.
So, what do we do next?
Producing lithium using conventional evaporation ponds poses several environmental and social challenges. Deploying more holistic and innovative processes, such as DLE and counter flow reverse osmosis–based technology, combined with advanced brine aquifer subsurface engineering, provides an opportunity to recover 85% to 95% of the available lithium and reinject about 90% of spent brine back into the reservoir. Similarly, the smaller footprint required by these sustainable lithium production processes reduces anthropogenic changes at the surface.
By implementing these technologies, producers can play a significant role in minimizing the impact on local hydrogeology, reducing water stress, sustaining biodiversity in these unique ecosystems, and ensuring that we don’t play a zero-sum game on our quest to supply enough lithium to meet electrification demand.