The world is at a difficult juncture. Approximately 15% of the global population lives in energy poverty (without access to electricity), facing devastating consequences. And energy demand will only increase as the world’s population grows. According to the 2023 Energy Outlook from the U.S. Energy Information Administration, primary energy demand is projected to increase from 16% in 2022 to 57% by 2050 depending on various scenarios.
In the early 1990s, the first Intergovernmental Panel on Climate Change (IPCC)—the United Nations body for assessing the science related to climate change—warned that climate change effects would soon be seen. Global surface temperature data, recorded since 1850, shows that temperatures have risen by 1.1 degC. It’s predicted that with no climate change policies and actions, temperatures may increase even more from 4.1 degC to 4.8 degC. Such a change will bring more extreme weather events and rising sea levels, which is important considering that 10% of the world’s population lives in areas less than 10 meters above sea level.
Climate models cannot accurately explain the observed temperature increases without considering anthropogenic causes of carbon dioxide emissions. CO2 and methane are the predominant greenhouse gases (GHG) driving this change, with most emissions coming from fossil fuels and industrial activity. GHGs prevent some of the energy reflected from Earth to space, putting the global system out of equilibrium and raising temperatures.
Well interventions on existing assets can stimulate production by increasing both daily output and the recovery factor. I recently demonstrated how a 10% production increase is not only very achievable but could also reduce the pressure to invest in additional infrastructure and the drilling of new wells. As you can see in the visual below, each of these additional investments comes with its own CO2 footprint—a footprint that could potentially be avoided.
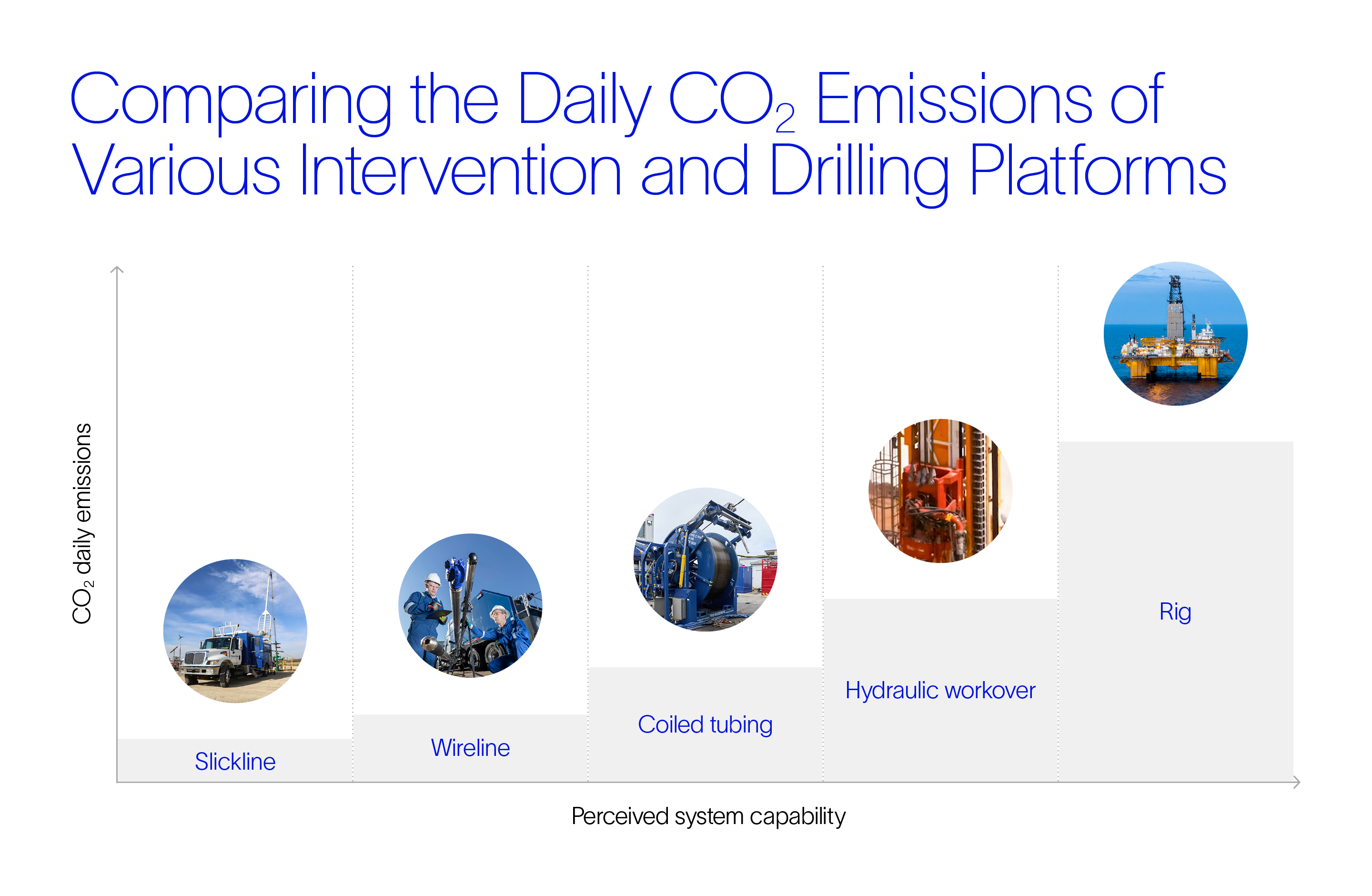
In fact, one of my recent technical papers provided detailed, quantifiable emission rates for various delivery platforms, with slickline systems producing the lowest emissions—ranging from 0.89 metric tons over a 24-hour period to 30–150 metric tons in the same period while drilling a rig (which generates the highest emissions). This means that every time we utilize smaller, more efficient systems or approaches, emissions savings are maximized.
Well intervention is one of those approaches. It’s a critical component of improved oil recovery (IOR) and can even be taken a step further with enhanced oil recovery (EOR) efforts. If considered during the creation of the initial field development plan, these strategies can make all the difference for both operator and environment.
Innovation drives lighter delivery platforms forward
Significant improvements have been made in the performance of legacy intervention and drilling systems. Meanwhile, the traditional separation of intervention techniques by conveyance systems has been greatly reduced, thereby allowing lighter platforms to achieve similar outcomes in multiple scenarios, as visualized below.
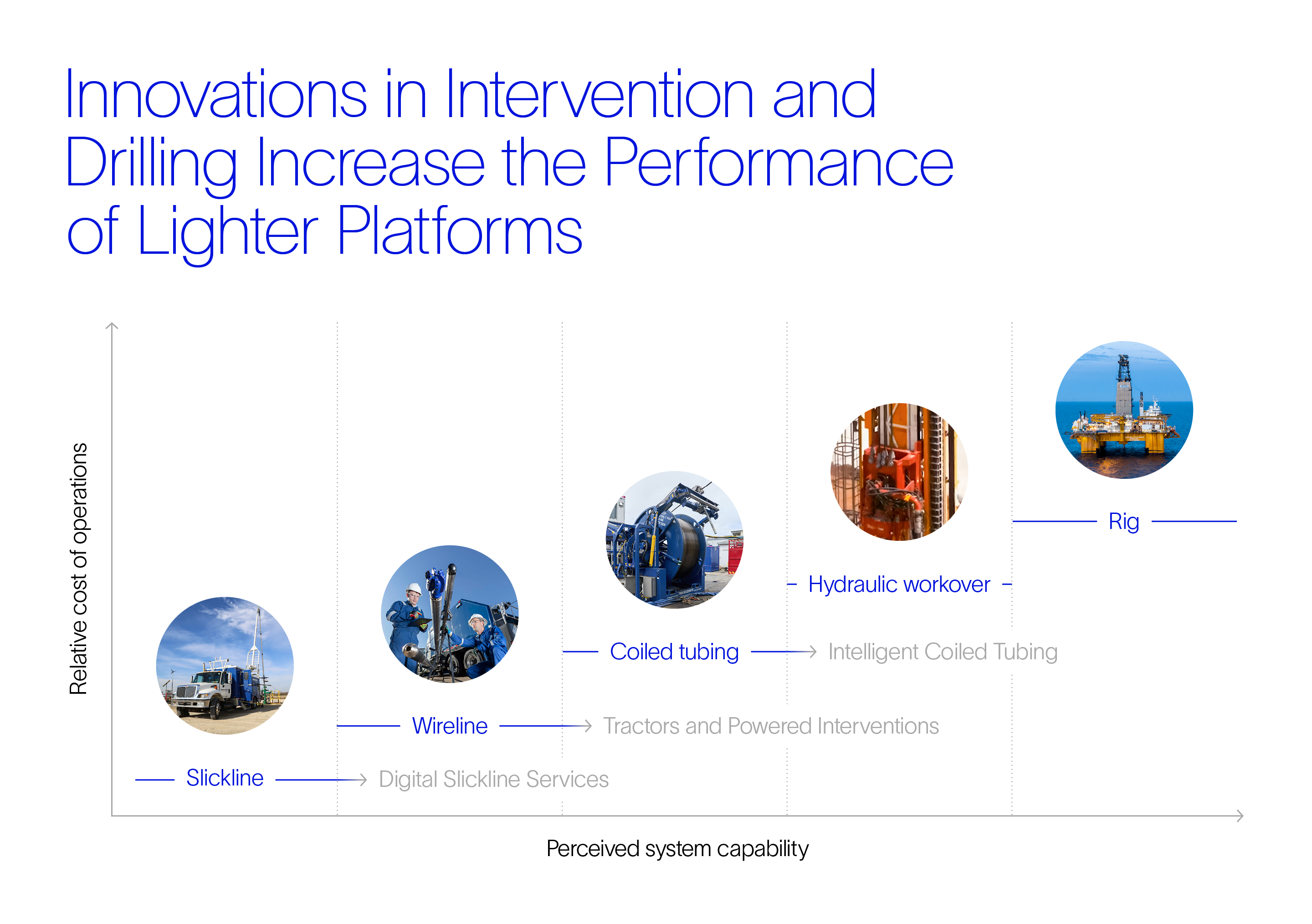
One example is the use of digital slickline (DSL). Historically, electric line and slickline services have been very disparate. Electric lines could not be jarred without risking damage to the electrical insulation or mechanical failure due to the torquing of the armor wires. In contrast, slickline (being smaller and requiring simpler pressure control) offered many advantages but could not be used for surface readout during electric line logging operations. Years ago, conductive slickline—a 0.160-inch tubing encapsulated cable—was introduced, but it lacked the strength for slickline mechanical operations and thus had limited application.
Digital slickline tech has since evolved. Today’s versions feature a standard core slickline cable with a polymer coating and can perform mechanical work while also enabling surface readout logging.
Digital slickline tech for production logging has been successfully implemented in the oil fields of southeast Kuwait, enabling Kuwait Oil Company to significantly reduce deferred production and operational costs without compromising on data quality. It also transformed how the organization performed surveillance operations through a more efficient workflow.
A detailed analysis of more than 11 wells where production logging was conducted with DSL revealed significant improvement. Compared with conventional workflows, DSL implementation saved approximately 51,000 barrels of deferred oil production and improved operational efficiency by 72%, all without compromising real-time data quality or that during interpretation stages.
A new age of wireline milling
In the evolution of electric line capabilities, powered intervention tools offer a clear example of achieving more with a smaller surface footprint. Powered intervention on electric lines refers to using tools such as linear actuators, intelligent shifting tools, wellbore debris cleanout tools, and wireline machining.
Only a decade ago, the prospect of being able to mill on wireline was deemed niche. Traditional pipe-based milling benefits from hydraulic power and circulation to remove cuttings, but this is not inherently available on wireline. Advances in downhole instrumentation, however, have recently led to a step change in capabilities.
Milling can be broken down into two broad sections:
- the milling of wellbore debris (via buildup or scale)
- the milling of completion accessories themselves (e.g., nipples and valves)
In the case of wellbore debris, mitigation can often be achieved by either having cuttings drop to the bottom (if the deviation and passage for cuttings through the scale makes this possible) or by flowing the well at a suitable rate to lift the cuttings.
Milling completion accessories, on the other hand, are more challenging due to cuttings’ material hardness and differing nature. Without the use of reverse circulation junk baskets or the ability to circulate to the surface, minimizing cuttings becomes critical—which is why the use of annular cutters (versus traditional junk mill approaches) is more advantageous.
For example, when milling through a wellbore valve with a junk mill, all the material at the face of the mill must be ground away. The grounded area is significantly reduced, thereby reducing cuttings and the energy required to make a cut. That said, the unmilled section within the cutter does need to be retained, for which innovative “coupon” catchers have been developed.
Additionally, the milling action no longer requires circulation, which can potentially damage the formation. Milling times can be optimized as the milling bit is centralized—typically by a wireline tractor or anchor—to reduce shock or bit whirl on the milling target.
Downhole automation (visualized below) can also be leveraged to further optimize the process. This visualization of the evolution of wireline milling tech shows advancements from the basic use of cable tension to the more advanced surface computer control, culminating in the fully automated linear actuator machining (which has proven to reduce milling time by up to 50%).
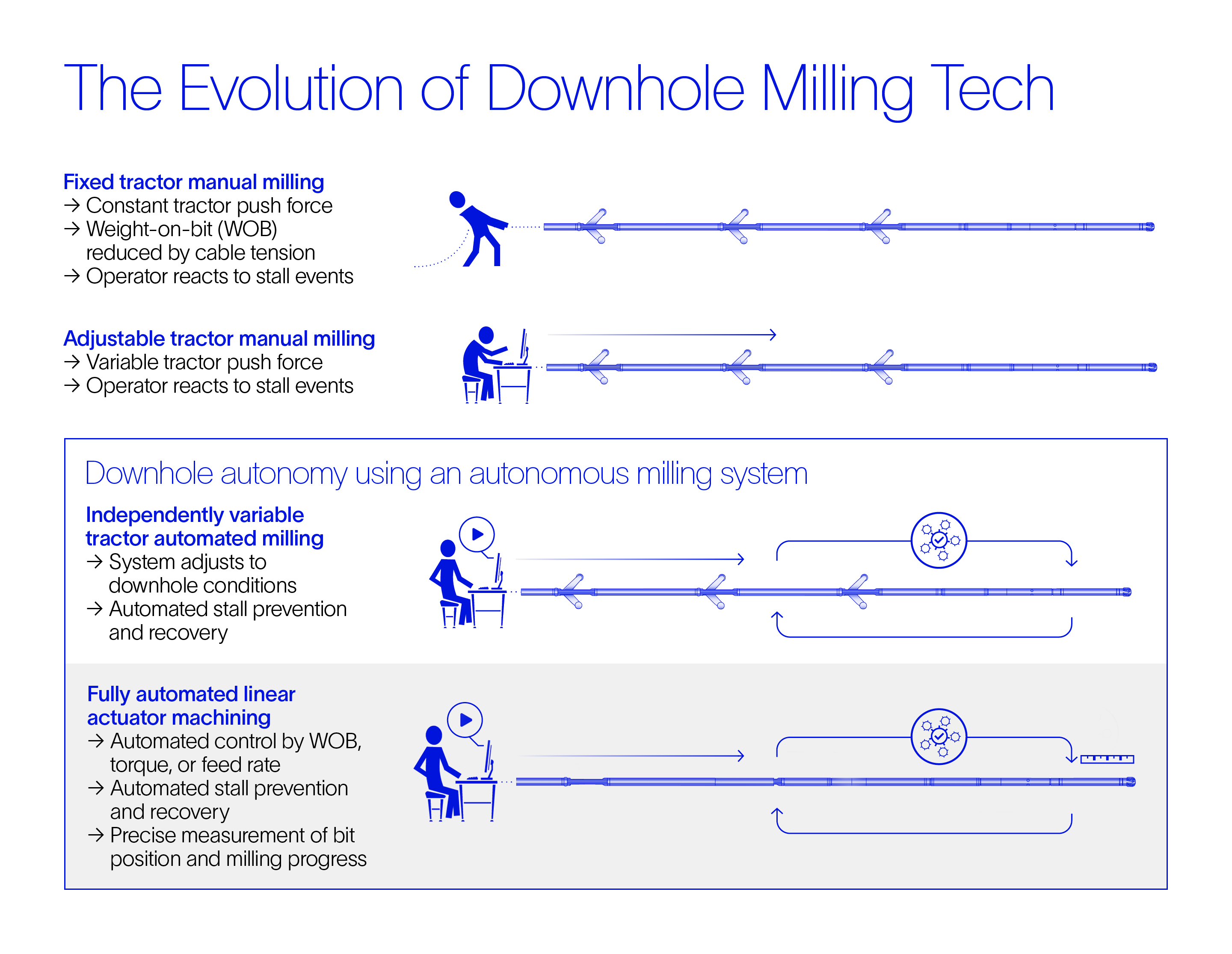
With the coordinated control of an autonomous milling system, the tractor and milling tool operate as a single intelligent system to maximize milling efficiency and ensure operation success. This system eases dependency on the engineer's intervention, unlike existing wireline milling tools that need an experienced engineer to constantly monitor and adjust milling parameters.
Such systems were first introduced for tractor WOB control and have since increased in WOB, as well as precision capability, thanks to linear actuated-based control. So much so that the term “machining” (as opposed to “milling”) is being used due to the higher level of control and precision now available.
While not suitable for all applications, wireline milling shows promising results when used in the right environment. It can be applied on an intervention vessel to mill through a partially open ball valve, generally performing the milling operation in just 40 minutes. And it’s also known for its potential to double production with increases along the lines of 5,500 barrels per day achieved from a wireline package.
Turning to coiled tubing where wireline is not an option
When wireline is not feasible, coiled tubing is an alternative that can likely perform the operation. In Norway, for example, conventional coiled tubing operations are known to be time consuming, with an average of 10 to 14 days required to spot equipment and rig up. Weather dependency, platform crane priorities, deck occupancy, kit positions (requiring 60 to 70 lifts and 250 square meters), and other platform activities all contribute to the complications. This generally results in lengthy and costly operations. Furthermore, the use of diesel-powered equipment, such as power packsand fluid pumps, can generate CO2 emissions as high as 930 kilograms per hour.
Recognizing that not all coiled tubing operations require the use of a full coiled tubing package—with the associated size of power stand, reel, and coil tubing string—an alternative, more efficient option was developed: the light string unit (LSU). LSUs can deploy coiled tubing strings up to a maximum diameter of 2 inches into depths of up to 5,500 meters. This system has nearly halved the number of lifts needed, with all modules weighing less than 15 metric tons and minimized to fit through a 2.3 m x 4.5 m hatch.
The hydraulic power unit is now also electrically powered, thereby reducing CO2 production significantly. And while it doesn’t have the full capability of a larger system, an LSU can perform mechanical operations such as cleanouts, plug setting and sleeve manipulation, logging, perforating, preplug and abandonment workflows, nitrogen lifts, stimulation, and zonal isolation. This setup gives operators the flexibility to deploy faster and with shorter campaign durations.
An LSU can also be equipped with real-time downhole coiled tubing tech, which allows surface data to be read out from downhole borehole assemblies. This enhances efficiency gains as the program can be changed on the fly in response to actual downhole conditions.
Coming up next
The aforementioned scenarios are only some examples of how intervention operations can simultaneously increase production, increase recovery factors, and reduce footprint and CO2 emissions compared with drilling new wells or using conventional intervention methods. In a world where balancing energy requirements with the need to reduce GHG emissions is mission critical, interventions provide a valuable opportunity.
What we have yet to address is how interventions also reduce GHG well leaks, at the source, when caused by the likes of sustained casing pressure and bradenhead pressure—topics that I will cover in the next part of this series.
Stay tuned!